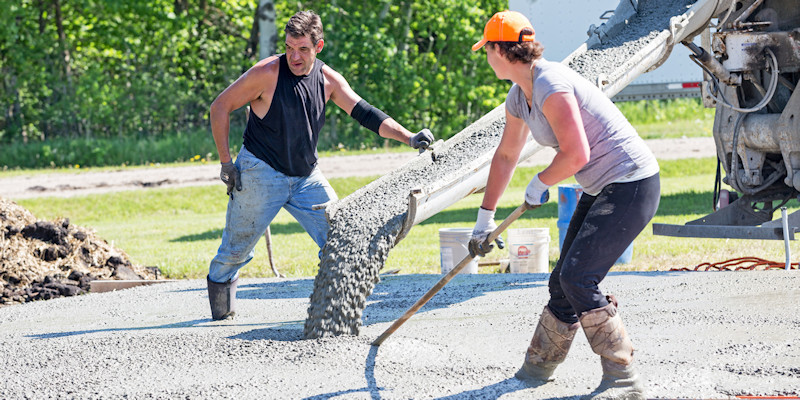
Concrete! It has been used since before 6,500 BC, most extensively in the Roman Empire, and then forgotten until it’s resurrection in Europe around the 15th century. Today it’s the most prevalent man-made material on the planet — used for homes, high rises, roads, bridges, and parking lots — and for good reason. It provides strength, flexibility, and durability in construction that is matched by few if any other building materials.
The Number One Source of Embodied Carbon in Buildings
The cement used in concrete is produced by burning limestone in kilns at very high heat (2,300° to 3,000° F) usually using powdered coal or natural gas as fuel, wasting a great deal of energy and releasing carbon dioxide (CO2) from the combustion. The chemical reaction involved in making cement releases more CO2 as a byproduct. Producing one ton of Portland cement produces one ton of CO2 emissions. Seventy-nine percent of concrete’s CO2 emissions come from the cement even though it is only 13% of the material – the rest is sand, aggregate, and water.
It’s not surprising that concrete is the number one source of embodied carbon in buildings – accounting for up to 55%. And it’s responsible for 8 to11% of global CO2 emissions. If it was a country, the concrete industry would be the third-highest emitter of CO2 after China and the United States. Yet it’s the “foundation” of homes, buildings, cities, and transportation systems throughout the world and its use is growing fast. Worldwide demand for concrete is second only to water.
How can we continue to take advantage of the strength, flexibility, and durability benefits of concrete while reducing its CO2 impact? And more importantly how can CO2 be used in concrete production to turn one of the worst sources of carbon emissions into a method to lock up carbon for the long term?
Using Rather than Storing CO2
CO2 capture and storage is the old way of thinking. The technology for sequestering (capturing and storing) CO2 from gas-fired power plants, cement, and fertilizer manufacturing is well established, but until now there have been few economic uses for the resulting product. Most of the focus has been put on underground storage. But to cost effectively meet important climate goals, we must move to CO2 “capture and use” – and, with recently available technology, concrete now provides a prime opportunity. CO2 from producing cement, or from other industrial processes, can be captured and added to ready-mix concrete or to its components, where it is converted to a mineral that can never be released as CO2. The resulting concrete is often stronger and uses less cement.
Green Concrete Technologies and Their Availability
Several companies currently use CO2 and/or reduce CO2 emissions in their products in different ways to produce “green” concrete products that range from somewhat lower carbon, to zero carbon and carbon negative. CarbonCure Technologies, a company based in Halifax, Nova Scotia, invented a process that involves removing CO2 from the creation of cement and injecting it into concrete during mixing. This takes some of the CO2 out of the air and permanently embeds it in the concrete and strengthens it – reducing the amount of cement needed. So far, CarbonCure concrete achieves a net carbon reduction of only 5 to 7%. Its strongest advantage is its widespread availability throughout North America. See their map of CarbonCure producers and ask your local supplier for it.
Blue Planet, based in Los Gatos, California, uses carbon dioxide collected from the exhaust stack of power plants to produce synthetic aggregate that can be used to create concrete. The captured CO2 from flue gas does not require purification, which is an energy and capital intensive process. As a result, Blue Planet’s method is extremely efficient, and results in a lower cost than traditional methods of CO2 capture. CO2 from flue gas is converted to carbonate (CO3), which locks up the carbon forever. The result is low carbon, carbon neutral, or carbon negative concrete, with the same structural integrity as conventional concrete. By offsetting the carbon footprint of the cement, the carbon sequestered in Blue Planet’s synthetic aggregate more than compensates for the cement component’s carbon footprint, making the combination net carbon neutral or negative. The process also reduces the need to further mine sand and limestone aggregates which are the major components of concrete and the cause of significant environmental impact. Although Blue Planet is still piloting its technology, Central Concrete in California, part of Texas-based U.S. Concrete, has already used Blue Planet aggregate in concrete poured at San Francisco International Airport. Blue Planet’s aggregate should be available to concrete producers by 2022. Check in with Blue Planet for availability updates.
CarbiCrete uses a process called carbonation activation that eliminates the need for cement in concrete by replacing it in the mix with ground slag, a waste by-product of steel-making. The concrete mix is poured into molds just like conventional concrete and is then cured using CO2 captured from industrial sources. During curing, the gas becomes a solid, binding together the slag granules, and giving the concrete its strength. The process can be implemented in any precast concrete manufacturing plant, but is not yet available for poured concrete applications. CarbiCrete’s process eliminates the CO2 emissions associated with cement production and then injects CO2 recovered from other industries into its products. Because more CO2 is consumed than emitted during the process, it is carbon-negative concrete. CarbiCrete masonry products should soon be available through Patio Drummond in Quebec and they will be expanding distribution in future years. Its ready-mix concrete product is still in development and may not be available for a few years. But it is worth checking in with CarbiCrete to access this carbon negative solution as soon as it is available.
United States Concrete uses several methods to lower the carbon footprint of its concrete — from using CarbonCure, to using high strength aggregate that lowers the need for cement, to incorporating fly ash from burning coal or steel slag into cement. Incorporating steel slag reduces Portland Cement usage by as much as 50%. It also can produce aggregate from slag. This reduces the amount of slag that becomes landfill waste and reduces the need to mine raw materials. U.S. Concrete has outlets on the east and west coasts, as well as in Texas. If one is near you, ask them if they have any of these low CO2 concrete options available. Or reach out to their California office for more information on their low CO2 concrete options.
Solidia Technologies in Piscataway, New Jersey uses a lower temperature, lower energy process, resulting in 30 to 40% less CO2 emissions during cement manufacture. In addition, it cures their concrete with waste CO2 instead of water, permanently trapping CO2. It claims a 70% overall reduction in CO2 emissions compared to standard precast blocks and conserves a great deal of water. Solidia concrete cures in less than 24 hours compared to 28 days for traditional concrete. Solidia’s low carbon concrete is available in pavers and blocks today in North America from EP Henry for landscaping, retaining walls, driveways, sidewalks, and patios. Solidia’s ready-mix will substitute some of its low carbon cementitious material for ordinary Portland cement and lower the carbon footprint of ready-mix by 30%. That should be available within the next two years. Check for availability with Solidia.
Geopolymer cement has been available for years. Rather than sequestering CO2, it uses no Portland cement at all, resulting in a very low carbon profile as well as having superior durability. Geopolymer Solutions in Texas makes a heat-free, geopolymer concrete that combines recycled waste from fly ash, ground granulated blast-furnace slag, and other naturally occurring minerals in place of using Portland cement. It has a carbon footprint that is about 10% that of Portland cement, is acid resistant, is much more durable and long lasting (up to 1,000 years according to the company) than standard concrete, and uses less water and virgin natural resources. The resulting cement is of higher quality than Portland cement and can be used at standard ready-mixed concrete facilities. It’s more expensive than standard concrete – but its benefits to the environment are many. Builders interested in using their product should call them directly or request that their concrete supplier call them.
Other Options
The cement industry is promoting a lower CO2 cement – Portland-limestone cement (PLC) which is a blended cement that incorporates between 5 and 15% limestone as an ingredient, lowering the amount of cement used in concrete and reducing its CO2 footprint by about 10%. Lehigh Cement of Canada produces concrete mixtures that incorporate EcoCemPLC which reduces the CO2 emissions by as much as 10%. You can locate North American Lehigh Cement suppliers here.